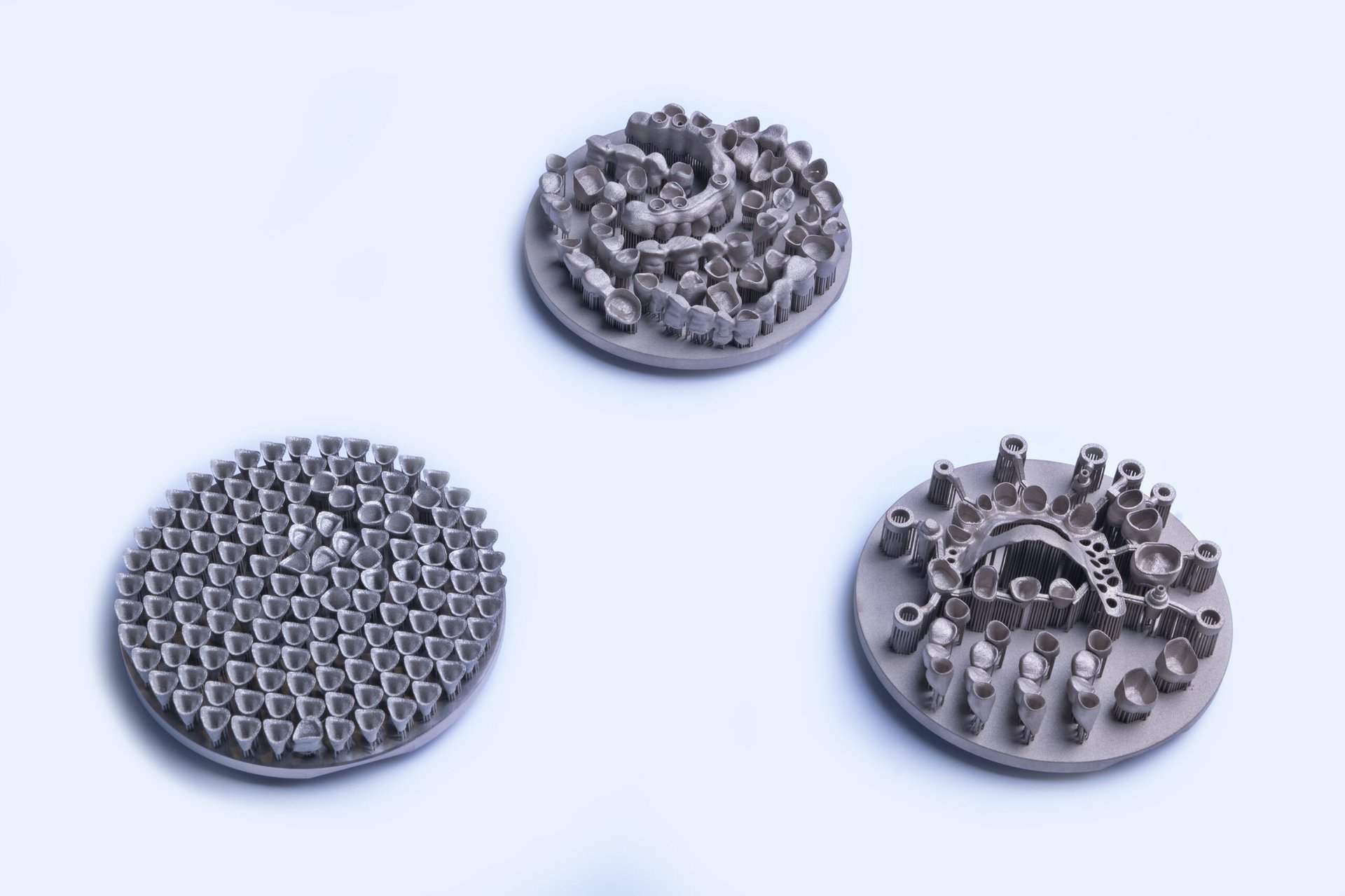
Metal Powder Materials
Wide Range of Materials
The choice of metal powder in 3D printing plays a pivotal role in determining the quality of the final output. Hence, selecting an appropriate material is crucial, and having a wide range of materials enhances the likelihood of achieving desirable outcomes. With ongoing advancements in additive manufacturing, new requirements surface, prompting research into the creation of specialized materials to meet these demands. The advent of these innovative techniques and the broad spectrum of materials made available by technological progress open up opportunities for breakthroughs in various domains.
Cobalt Based Alloys
CoCr28Mo6
The alloy you're referring to, which contains chromium, cobalt, and molybdenum, is a highly specialized material designed for use in both high-temperature industrial applications and the medical industry. Its unique combination of properties makes it suitable for a wide range of demanding applications. Here's an overview of its key material properties:
Exceptional Biocompatibility: This is a crucial property for any material used in the medical industry, particularly for implants and prostheses. Biocompatibility means that the alloy is non-toxic and not harmful to the human body. It does not cause an immune response, which makes it safe for long-term contact with human tissues.
Heat Resistance: The alloy's ability to withstand high temperatures without losing its structural integrity or properties is vital in applications such as jet engines. This heat resistance ensures that parts made from this material can perform reliably in environments where they are exposed to extreme temperatures.
Resistance to Thermal Fatigue: Thermal fatigue resistance refers to the material's ability to withstand the effects of cyclic heating and cooling, a common scenario in many high-temperature applications. This property is especially important in turbine parts and jet engines, where materials are repeatedly heated and cooled during operation.
Oxidation Resistance: The alloy's ability to resist oxidation, a form of corrosion that occurs when a material reacts with oxygen at high temperatures, is critical for its longevity and reliability. This property is particularly valuable in both the aerospace industry, where materials are exposed to high levels of oxygen at high altitudes, and in the energy sector, where components are often subjected to high-temperature environments.
The blend of exceptional biocompatibility with high heat resistance, resistance to thermal fatigue, and oxidation resistance makes this chromium-cobalt-molybdenum alloy an excellent choice for a variety of applications. In the medical field, its use in implants and prostheses is due to its safety and compatibility with the human body. In industrial applications like energy production and aerospace, especially in components like turbine parts and jet engines, its ability to perform under extreme conditions and temperatures is highly valued. This versatility across such diverse fields underscores the alloy's unique and valuable properties.
For other cobalt alloys please contact us
Aluminum Based Alloys
AlSi10Mg
This description pertains to a material commonly used in additive manufacturing, particularly favored by sectors like aviation, automotive, engineering, and in the production of heat exchangers. This material is chosen for its suitability in creating both prototypes and functional parts.
Key attributes that make it a preferred choice in these industries include its application in scenarios that demand both low weight and high mechanical properties.
The material is characterized by:
Very good corrosion resistance: This ensures durability and longevity, especially in harsh environmental conditions.
Good electrical conductivity: This property is essential for applications where electrical transmission is a factor.
High dynamic toughness: This indicates the material's ability to absorb energy and withstand impact or stress, making it ideal for dynamic, high-stress environments.
Excellent thermal conductivity: This is crucial in applications where effective heat dissipation or transfer is required, such as in heat exchangers or engine parts.
Given these properties, it's clear why this material is highly valued in sectors where the combination of strength, durability, and functional performance is critical.
AlSi7Mg
This material is an aluminum-based alloy that is frequently chosen for applications where excellent thermal conductivity and good fracture or stress resistance are required. It is particularly popular in fields like maintenance, automotive, heat exchanger production, research, and prototyping.
The properties of this alloy include:
Good electrical conductivity, making it suitable for electrical applications.
Excellent machinability, allowing for ease of shaping and manufacturing.
Good resistance to changes, ensuring stability under various conditions.
Good strain tolerance, meaning it can withstand mechanical stress without deformation.
Excellent thermal conductivity, which is ideal for managing heat in various applications.
These characteristics make this aluminum-based alloy a versatile and reliable choice for a wide range of industrial applications.
AlSi9Cu3
This is an alloy composed of aluminum, silicon, and copper, known for its suitability in applications that demand performance at both high and low temperature extremes as well as across a broad range of temperatures. It's a preferred material in sectors like maintenance, automotive, heat exchanger production, research, and prototyping.
The alloy is characterized by several key material properties:
Excellent machinability, which makes it easy to work with in manufacturing processes.
Good electrical conductivity, beneficial for various electrical applications.
Good performance at high temperature limits, indicating its stability and functionality under high-heat conditions.
High thermal conductivity, ensuring efficient heat transfer, which is essential in applications like heat exchangers.
These attributes make this aluminum-silicon-copper alloy a versatile and effective material choice for a wide array of industrial uses, especially where temperature resilience and efficient heat management are required.
Titanium Based Alloys
Ti6Al4V ELI (Grade 23)
Ti6Al4V ELI (Grade 23) is a titanium alloy recognized as the high purity version of Ti6Al4V (Grade 5), which holds the distinction of being the most extensively utilized titanium alloy globally. This particular variant of the alloy is frequently chosen for manufacturing components in sectors such as energy, aerospace, automotive, and medical or biomedical applications, owing to its advantageous properties.
The material properties of Ti6Al4V ELI (Grade 23) include:
Good Corrosion Resistance: This property makes it highly durable and resistant to degradation in harsh environments, which is particularly valuable in aerospace and medical applications.
High Specific Power: The alloy's strength-to-weight ratio is significant, making it ideal for applications where weight reduction without sacrificing strength is crucial, such as in aerospace and automotive industries.
High Cycle Fatigue Strength: This attribute indicates the alloy's ability to withstand repeated stress over many cycles without failure, essential for components in energy and aerospace applications that undergo regular stress.
High Toughness: The material's ability to absorb energy and withstand impact and stress makes it suitable for use in robust and demanding environments, such as in aerospace and automotive parts, as well as in durable medical implants.
Overall, the combination of these properties makes Ti6Al4V ELI (Grade 23) a preferred choice in industries where reliability, durability, and high performance under stress and in challenging environments are paramount.
Ti (Grade 1+2)
Titanium Grade 2, often referred to as commercially pure titanium, is known for its versatile properties which make it suitable for various applications across different industries. Here's an overview of its key material properties:
Perfect Biocompatibility: This property is crucial in medical and clinical applications. Titanium Grade 2 is highly biocompatible, meaning it is non-toxic and not rejected by the human body. This makes it an ideal material for medical implants, dental applications, and surgical instruments.
Excellent Corrosion Resistance to Seawater: This feature is particularly significant in the chemical, petrochemical, and marine industries. The alloy's resistance to corrosion by seawater means it can be used in environments where exposure to saline or corrosive substances is a concern.
Good Ductility: Titanium Grade 2 has the ability to deform without losing toughness or strength. This ductility makes it useful in applications where some degree of flexibility or bending is required, without the risk of fractures.
Medium Strength: While it is not as strong as some of the higher grades of titanium, Grade 2 strikes a balance between strength and ductility, making it suitable for a wide range of applications.
Good Mechanical Properties: This encompasses a combination of strength, ductility, and resistance to fatigue and crack propagation. These properties are essential in applications subjected to mechanical stresses, such as components in energy and aerospace industries.
High Strength-to-Weight Ratio: Despite its medium strength in absolute terms, when compared to its weight, Titanium Grade 2 is very strong. This high strength-to-weight ratio is valuable in applications where reducing weight while maintaining strength is important, such as in aerospace and automotive design.
Low Density: The low density of Titanium Grade 2 makes it lighter compared to many other metals, contributing to its high strength-to-weight ratio. This property is particularly beneficial in industries like aerospace and automotive, where reducing the overall weight of components can lead to improved efficiency and performance.
Overall, the combination of biocompatibility, excellent corrosion resistance, good ductility, and a favorable strength-to-weight ratio make Titanium Grade 2 a versatile and widely used material in industries ranging from medical and clinical to energy, chemical/petrochemical, and heat exchanger applications. Its ability to perform well in both harsh chemical environments and in human bodies highlights its unique adaptability.
Nickel Based Alloys
HX
The nickel-based alloy you're describing, characterized by high percentages of chromium, molybdenum, and iron, is indeed a specialized material designed for demanding applications. Its material properties make it particularly suited for high temperature and abrasive environments. Here's a closer look at each of these properties:
High Strength: This alloy is known for its exceptional strength, particularly under high-temperature conditions. This strength is crucial in applications where the material must maintain its integrity under significant stress and load.
Good Ductility: Despite its strength, this alloy also maintains good ductility. Ductility refers to the material's ability to deform under tensile stress, which is important in applications where the material must endure bending, shaping, or drawing without cracking.
Excellent Oxidation Resistance: High oxidation resistance is a key property for materials used in high-temperature environments. This means that the alloy can withstand exposure to oxidizing conditions at elevated temperatures without degrading, making it ideal for use in applications like turbine parts and other components in the aviation and energy sectors.
High Yield Strength up to 850°C: Yield strength is the stress at which a material begins to deform plastically. The fact that this alloy maintains high yield strength up to 850°C indicates its suitability for use in environments where it will be subjected to extremely high temperatures. This is particularly relevant in industries like aviation, energy, and the chemical industry, where materials are often exposed to high thermal stress.
The combination of these properties - high strength, good ductility, excellent oxidation resistance, and high yield strength at elevated temperatures - makes this nickel-based alloy an excellent choice for abrasive, high-temperature applications. Its ability to perform reliably in challenging conditions makes it a preferred material in fields like aviation, energy, and the chemical industry, particularly for components like turbine parts that require a high degree of durability and thermal stability.
IN625
IN625, a precipitation hardening nickel-based alloy alloyed with chromium, molybdenum, and niobium, is indeed a highly specialized material chosen for its unique properties. These properties make it particularly suitable for aircraft engine components and various applications in the aerospace, energy, chemical industries, and in the manufacturing of turbine parts. Let's delve into each of its key material properties:
High Strength: IN625 is known for its exceptional strength, which is a critical attribute for materials used in high-stress environments such as aircraft engines. This high strength ensures that the components can withstand the intense forces they are subjected to during operation.
Good Ductility: Despite its high strength, IN625 maintains good ductility. This means it has the ability to deform without losing its toughness, which is essential in applications where the material needs to handle bending and shaping processes without cracking or failing.
Excellent Creep Rupture Strength Below 700°C: Creep rupture strength refers to the material's ability to resist deformation or failure over a prolonged period under high temperature and stress. IN625's excellent creep rupture strength below 700°C makes it ideal for aircraft engine components and other high-temperature applications where materials are continuously exposed to stress and high temperatures.
Excellent Resistance to Oxidation and Corrosion: IN625 exhibits superior resistance to oxidation and corrosion, making it suitable for use in harsh environments. This property is particularly valuable in the aerospace and chemical industries, where materials are often exposed to corrosive substances and extreme temperatures.
The combination of high strength, good ductility, excellent creep rupture strength, and outstanding resistance to oxidation and corrosion makes IN625 a highly desirable material for applications that demand reliability and performance under extreme conditions. Its suitability for use in environments with temperatures up to 650°C, along with its robustness in facing mechanical and thermal stress, makes it a preferred choice in the aerospace industry, particularly for aircraft engine components, as well as in the energy and chemical sectors for various high-performance applications.
IN718
The nickel-chromium alloy you're describing, known for its precipitation hardening capabilities, is highly valued in industries that demand materials capable of withstanding extreme conditions, such as high temperatures. Its use in aircraft engines, gas turbines, and other high-temperature applications underscores its robustness. Let's explore its key material properties in detail:
High Strength: This alloy's high strength is a critical feature for applications that are subjected to extreme forces and stresses. In aircraft engines and turbines, materials must maintain structural integrity under significant mechanical stress, and this alloy's high strength ensures reliability in these demanding conditions.
Good Ductility: The good ductility of this alloy means that it can be deformed (bent or stretched) without losing its toughness or breaking. This property is essential for manufacturing processes that require shaping or molding the material, and for applications where the material might experience bending or stretching forces during operation.
Excellent Build Resistance: This property indicates the alloy's ability to resist changes in structure and properties over time, particularly in high-temperature environments. This stability is crucial for components in aerospace and energy applications, where materials must maintain their integrity over long periods and under varying conditions.
Excellent Mechanical Properties up to 700°C: The alloy exhibits exceptional mechanical properties - including tensile strength, creep resistance, fatigue life, and rupture strength - at temperatures up to 700°C. This makes it especially suitable for high-temperature applications.
Tensile Strength: This refers to the resistance of the material to breaking under tension.
Creep Resistance: Important in high-temperature applications, this is the material's ability to resist gradual deformation under constant stress.
Fatigue Strength: The endurance of the material under repeated cycles of stress.
Rupture Strength: The ability to withstand breaking or failing under prolonged stress.
The combination of high strength, good ductility, build resistance, and excellent mechanical properties at elevated temperatures makes this nickel-chromium alloy ideal for use in aerospace (particularly in aircraft engines), energy, and chemical industries, as well as in the manufacturing of turbines. Its ability to perform reliably under extreme conditions and high temperatures is why it's a preferred material for these challenging applications.
Iron Based Alloys
316L
Stainless steel 316L, known for its austenitic structure and high chromium content, is widely recognized for its exceptional properties, making it suitable for a variety of applications across diverse industries. Let's delve into its key material properties:
Very Good Corrosion Resistance: One of the standout features of stainless steel 316L is its excellent resistance to corrosion, particularly in chloride environments. This makes it ideal for use in conditions where exposure to corrosive elements, such as saltwater or chemical agents, is a concern. Its corrosion resistance is a primary reason for its use in the aerospace and automotive industries, offshore installations, and the food industry, where materials are often exposed to harsh chemicals or saline conditions.
High Strength at High Temperatures: Stainless steel 316L maintains its strength even at elevated temperatures. This property is crucial in applications where the material will be subjected to high thermal stress. It ensures that components made from this steel can withstand the rigors of high-temperature environments, such as those found in aerospace applications and automotive engines.
High Ductility: The high ductility of 316L means it can be deformed (bent or stretched) without losing toughness or breaking. This property is particularly important in the manufacturing process, allowing for the creation of complex shapes and forms without compromising the material's integrity. High ductility also contributes to the material's performance in demanding applications, such as in surgical instruments, where precision and reliability are key.
The combination of very good corrosion resistance, high strength at elevated temperatures, and high ductility makes stainless steel 316L a versatile and highly sought-after material. Its suitability for use in environments that are corrosive, high in temperature, or require precise and reliable mechanical properties underlines its widespread use in the aerospace and automotive industries, in surgical instruments, the food industry, and offshore installations. This versatility is a testament to its well-balanced composition and austenitic structure, making it a preferred choice for many demanding applications.
1.4828
The austenitic stainless steel you're referring to, known for its high strength and exceptional anti-scaling properties at temperatures up to 1000°C, is indeed a specialized material designed for high-temperature applications. Its unique properties make it suitable for various demanding environments, particularly in the automotive, machinery, and oven manufacturing industries. Let's explore its key material properties:
Austenitic Stainless Steel: Austenitic stainless steels are known for their high chromium and nickel content, which contributes to their excellent corrosion resistance and good mechanical properties. This microstructure makes them non-magnetic and typically less brittle at low temperatures. They are also known for their good formability and weldability, making them versatile for various manufacturing processes.
High-Temperature Resistance Up to 1000°C: One of the standout features of this steel is its ability to withstand very high temperatures without losing its structural integrity. This property is crucial for components used in environments with extreme thermal conditions, such as in high-temperature ovens and certain automotive applications where parts are exposed to sustained high temperatures.
High Strength and Scale Resistance at High Temperatures: In addition to its high-temperature resistance, this steel also maintains high strength at elevated temperatures. Its anti-scaling property is particularly important, as it resists the formation of oxide layers (scale) that can form on the surface at high temperatures. This scaling can compromise the material's structural integrity and lead to failure or reduced efficiency in many applications.
The combination of being an austenitic stainless steel with high-temperature resistance up to 1000°C and the ability to maintain high strength and scale resistance at these temperatures makes this material highly suitable for load-bearing components in high-temperature environments. Its typical applications in automotive components, machinery, and ovens, where reliability and performance under extreme temperature conditions are critical, highlight its specialized and valuable properties. This steel's unique capabilities ensure its preferred use in applications where standard stainless steels might not perform adequately.
1.2709
Maraging tool steel, particularly the type you're describing with high amounts of alloyed nickel and some molybdenum, is a specialized material known for its unique combination of properties. It's favored in various demanding applications such as injection molding, engineering parts, and in the automotive and aviation fields. Let's delve into its key material properties:
Martensitic Hardening: Maraging steels are known for their martensitic hardening process. Unlike traditional steel hardening, which involves rapid cooling (quenching) from high temperatures, maraging steel is hardened by a relatively low-temperature heat treatment that transforms the steel to a martensite structure. This process contributes to the steel's strength and toughness without significantly reducing ductility.
High Toughness: One of the standout features of maraging steel is its high toughness. Toughness refers to the material's ability to absorb energy and deform without fracturing, making it extremely resilient against impact and shock loads. This property is particularly important in applications that require durability and resistance to sudden or unpredictable stresses, such as in automotive and aviation components.
High Tensile Strength: Maraging steels are characterized by their high tensile strength, which is the maximum amount of stress (tension) that a material can withstand while being stretched or pulled before necking (when the specimen's cross-section starts to significantly contract). This high tensile strength makes maraging steels ideal for heavy-duty applications where the material must endure substantial loads without failing.
Performance at Elevated Temperatures (up to 400°C): While maraging steels are generally not known for their high-temperature performance, the particular type you're referring to maintains its properties up to 400°C. This makes it suitable for applications where the material will be exposed to elevated temperatures, though not as high as some other heat-resistant materials.
The combination of martensitic hardening, high toughness, high tensile strength, and the ability to maintain properties at temperatures up to 400°C makes this type of maraging steel particularly well-suited for demanding applications in injection molding, engineering parts, and the automotive and aviation industries. Its ability to endure significant stress and impact while maintaining integrity and performance under elevated temperatures underscores its specialized and valuable role in these fields.
H13 (1.2344)
H13 (1.2344) is a widely recognized martensitic tool steel that contains chromium, known for its significant strength and toughness. This steel is especially favored in tooling applications where these properties are crucial, such as in injection molding and various tooling areas. Let's explore its key material properties:
High Tensile Strength: H13 steel is characterized by its high tensile strength, meaning it can withstand significant stress or force without breaking or deforming. This property is essential for tooling applications where the steel must endure heavy and repeated loads. High tensile strength ensures that tools made from H13 steel can maintain their shape and functionality over prolonged use, even under strenuous conditions.
Moderate Corrosion Resistance: While H13 is not as resistant to corrosion as some other steels (like austenitic stainless steels), it does offer moderate corrosion resistance due to its chromium content. This level of resistance is generally sufficient for many tooling and industrial applications, particularly where the primary concerns are strength and toughness rather than extended exposure to corrosive environments.
Resistant to Thermal Fatigue Cracking: One of the notable features of H13 steel is its resistance to thermal fatigue cracking. This property makes it particularly suitable for applications involving cyclic heating and cooling, which is a common scenario in injection molding and other tooling processes. Thermal fatigue cracking occurs when materials are repeatedly heated and cooled, causing expansion and contraction that can lead to cracks and failure over time. H13's resistance to this phenomenon ensures a longer service life for tools and components made from this steel, even in environments with significant thermal cycling.
The combination of high tensile strength, moderate corrosion resistance, and resistance to thermal fatigue cracking makes H13 (1.2344) tool steel a popular choice in the manufacturing of tools and dies, particularly for high-stress applications like injection molding. Its ability to perform reliably under heavy loads and in environments with thermal cycling underscores its suitability for demanding industrial applications.